Although carbon is typically present in trace amounts in tungsten-nickel-iron alloy, its influence on alloy performance is significant. Carbon exhibits a "double-edged sword" effect: small amounts enhance strength and hardness through solid-solution strengthening and carbide dispersion strengthening, while excessive carbon reduces toughness and fatigue resistance due to brittle phase precipitation and interface weakening.
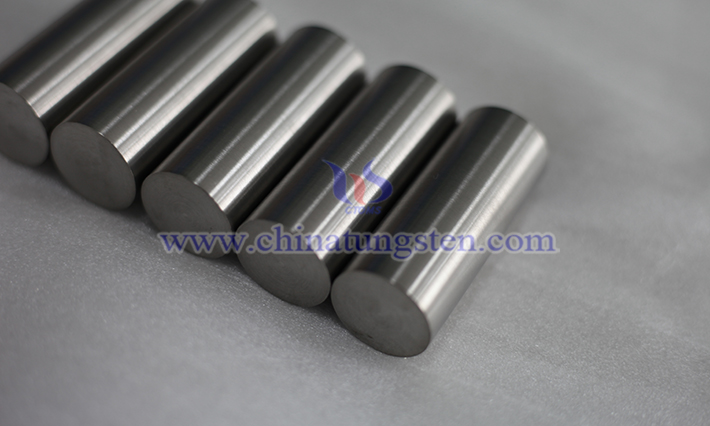
CTIA GROUP LTD Tungsten Nickel Iron Tungsten Alloy Picture
Carbon element primarily exists as an impurity in tungsten-nickel-iron alloy, originating from residual carbon in raw powders (e.g., trace carbon in tungsten powder), contamination during preparation, or the introduction of reducing agents like coke. With its small atomic size, carbon tends to segregate at the interface between tungsten particles and the nickel-iron binder phase, forming carbides or affecting interfacial bonding strength. The presence of these interfacial carbides can decrease the alloy’s toughness and fatigue resistance.
Under specific conditions (e.g., high-temperature sintering or excessive carbon source addition), carbon may react with tungsten to form tungsten carbides (WC or W?C). These carbides, harder than the tungsten matrix, enhance wear resistance and hardness via dispersion strengthening. However, excessive carbide formation leads to uneven microstructures, coarsened tungsten grain sizes, and reduced plasticity and impact toughness. High carbon content also lowers alloy ductility, increasing the likelihood of cracking during processing.
The nickel-iron binder phase is particularly sensitive to carbon content. Carbon can dissolve into the nickel-iron matrix, forming interstitial solid solutions that boost the binder’s strength and hardness, provided the carbon level remains low. However, exceeding the solubility limit prompts the precipitation of carbon-rich phases in the binder, causing embrittlement and reducing overall toughness. Additionally, carbon may affect the binder’s wetting of tungsten particles, indirectly altering tungsten distribution and alloy densification.
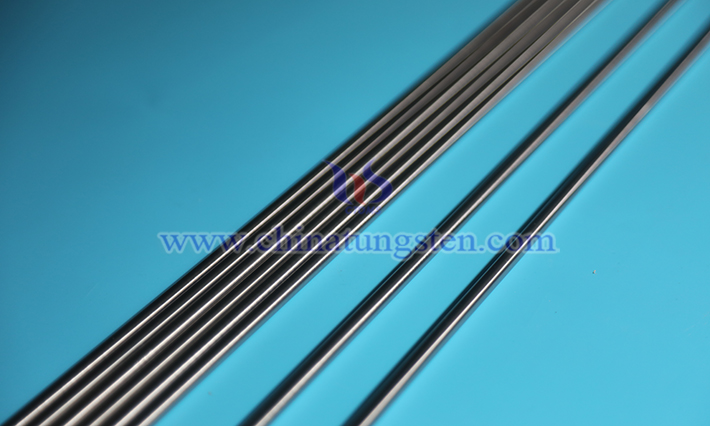
CTIA GROUP LTD Tungsten Nickel Iron Tungsten Alloy Picture
In practical applications, carbon content can be controlled below critical thresholds through raw material purification, process optimization, and microstructural regulation, combined with alloy design to optimize performance.
Raw Material and Process Optimization:
Powder Purity Control: Use high-purity tungsten and nickel-iron alloy powders to minimize carbon impurities.
Sintering Atmosphere Management: Conduct sintering in vacuum or inert atmospheres to reduce hydrocarbon contamination.
Reducing Agent Selection: In scrap recycling or carbon reduction processes, control the addition of reducing agents like coke to prevent carbon excess.
Microstructural Regulation:
Secondary Heat Treatment: Use cyclic heat treatment to dissolve and redistribute carbides, refining the microstructure.
Deformation Strengthening: Employ rotary forging or hot extrusion to introduce high-density dislocations, suppressing carbide precipitation and improving interfacial bonding.
Composite Alloying: Add rare earth elements (e.g., La, Y) or other alloying elements (e.g., Co, Mo) to mitigate carbon’s detrimental effects.