The influence of carbon element on the corrosion resistance of tungsten-nickel-iron alloy is primarily mediated through its forms of existence (carbides, solid solution, or interfacial segregation) and its regulation of microstructure. This manifests as effects on electrochemical corrosion behavior, passivation film integrity, and corrosion morphology, with the impact varying depending on carbon content, corrosive environment, and alloy microstructure.
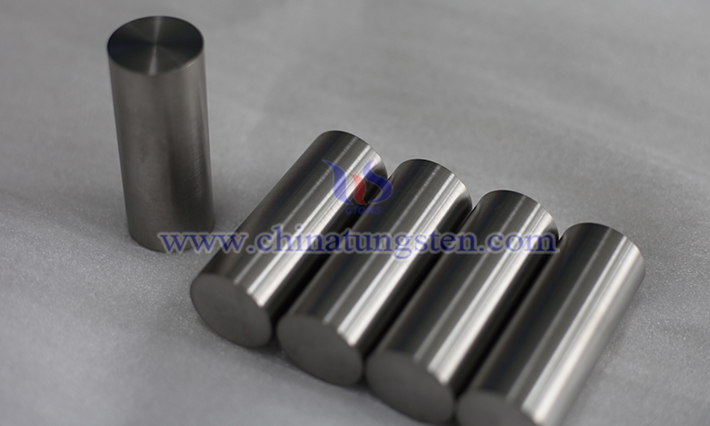
CTIA GROUP LTD Tungsten Nickel Iron Tungsten Alloy Picture
I. Mechanisms of Carbon’s Influence on Corrosion Resistance
Micro-Galvanic Corrosion Effect of Carbides
When carbon exceeds its solubility limit in tungsten-nickel-iron alloy, it readily forms brittle carbides (e.g., W?C or WC) with tungsten and iron. These carbides exhibit electrochemical differences from the matrix (tungsten particles and nickel-iron binder phase), acting as "cathodes" or "anodes" in micro-galvanic corrosion, accelerating localized corrosion. Corrosion Preference at Carbide/Matrix Interfaces: Lattice mismatches or stress concentrations at carbide-matrix interfaces often lead to easier rupture of passivation films (e.g., NiO) at these sites.
Interfacial Segregation’s Disruption of Passivation Film Continuity
As an interstitial element, carbon tends to segregate at the interfaces between tungsten particles and the nickel-iron binder phase (especially when diffusion is incomplete during sintering). This segregation inhibits the formation of a continuous passivation film in interfacial regions, creating "interfacial corrosion channels." Hindrance to Passivation Film Formation: The corrosion resistance of the nickel-iron binder relies on a dense Ni2?/Fe3? oxide film (passivation film). Interfacially segregated carbon adsorbs oxygen, competing with nickel and iron to form oxides—since carbon’s binding energy with nickel exceeds that of nickel with oxygen—preventing NiO formation and causing "discontinuities" in the passivation film. Expansion of Interfacial Corrosion: Once the interfacial passivation film ruptures, corrosive ions like chloride can penetrate preferentially, triggering delamination between tungsten particles and the binder phase.
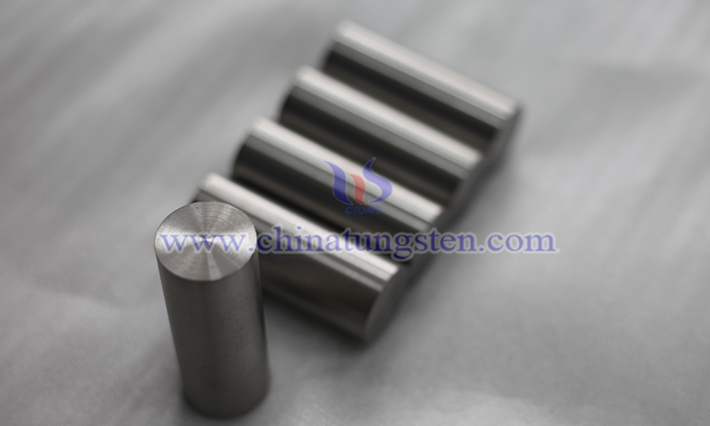
CTIA GROUP LTD Tungsten Nickel Iron Tungsten Alloy Picture
Impact of Carbon Content on Corrosion Product Stability
The structure and stability of corrosion products influence the alloy’s corrosion resistance, with carbon indirectly affecting the corrosion process by altering their composition and compactness. Positive Role of Low Carbon Content: Trace carbon dissolved in the nickel-iron binder can refine binder grain size, promoting a more uniform passivation film and reducing porosity in corrosion products. Negative Role of High Carbon Content: Excess carbon-formed carbides are prone to dissolution or detachment during corrosion, with their dissolution products combining with ions in the solution to form loose corrosion products, facilitating deeper penetration by the corrosive medium.
II. Environment Dependency: Variations Across Different Corrosive Media
The effect of carbon is not uniform and varies with the corrosive environment (e.g., pH, ion types): In acidic environments, low-carbon alloys maintain stable passivation films, exhibiting uniform corrosion, while high-carbon alloys experience faster carbide dissolution, with interfacial and uniform corrosion occurring simultaneously. In alkaline environments, low-carbon alloys show mild corrosion, primarily from slow binder phase dissolution; high-carbon alloys react with OH? to form soluble tungstates, accelerating corrosion.